Stainless steel certifications for fabricators provide reassurance for consumers that stainless steel products will meet high-the quality and safety standards forand be safe to use. There are two regulatory agencies: 1) The American Society of Mechanical Engineers (ASME), and 2) ISO 9001:2015. ASME The American Society of Mechanical Engineers (ASME) offers certification programs, including certification of a manufacturer or assembler’s quality control processes, according to their Boiler and Pressure Vessel Code (BPVC).
Adherence to ASME’s stringent standards means the stainless steel manufacturer meets national and international industry and legal safety codes for production of the specific certified product. Some of the products that ASME certifies include pressure vessels, power and heating boilers, and holding tanks. During inspections, an authorized ASME inspection agency will look at the quality of the manufacturer’s materials, design, and fabrication as well as the manufacturing process. They’ll review the manufacturer’s processes and quality control procedures. They’ll also look at the quality of the final product – including its strength. and surface finish. Any pressure rated vessel must be certified by ASME.
Surface finishing is especially important in food grade and medical grade stainless steel, which requires a super-smooth surface for sanitary reasons. Mechanical polishing, passivation and electropolishing processes can help create a micro-smooth surface, and ASME maintains strict standards for these processes as well. Another certification program for stainless steel fabricators is the ISO 9001:2015 Certification. ISO stands for International Organization for Standardization. Based in Switzerland, it brings. together over 160 national standards bodies to develop agreed-upon standards for quality control. ISO requires a manufacturer to have a strong customer focus, high-level motivation and involvement by upper management, defined processes that are clearly communicated to all employees, and a program for continual improvement. ISO procedures help streamline processes, educate employees, and eliminate repetitive errors.
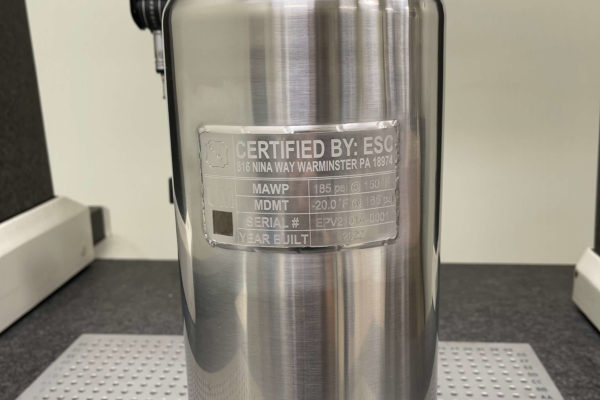
Stainless steel welding certification
Stainless steel welding certification helps ensure that a welder or fabrication company has the necessary skills to create a high-quality, durable welds that meets regulatory codes for a specific product. Professional welders begin their careers through apprenticeships that combine classroom education with on-the-job training – usually 144 hours of classroom training and 2000 hours on the job per year for 3-4 years. Welders may also start with a more formal education program at a community college or a trade or technical school, then go on to acquire experience. The next step is to become certified by passing a test with an authorized inspector.
The American Welding Society (AWS) offers certification testing at authorized testing facilities for both new welder certification and more advanced supervisor and inspector certifications. They also offer certifications in skill sub-categories for individuals and company certifications for stainless steel fabrication facilities. Eagle Stainless welders are required to pass several rigorous tests to earn their American Welding Society (AWS) Certifications. As well as Certificates, Eagle Stainless welders are also required to have qualifications above and beyond AWS requirements.
For example degrees, experience and/or exceptional skills. To pass an individual welding certification test, welders must demonstrate ability for the certification’s designated skill level and type. This includes their competency in the fit up, assembly, and positioning of the weld. Depending on the level of certification, welders may have to demonstrate competency in various welding positions, or methods, and practices. To stay certified, welders have to submit documentation that they are continuously welding still active welders every 6 months.
For a stainless steel fabricating company to earn welding certification, the company must undergo an on-site audit and demonstrate an adequate quality management program. Certifications are typically good for 3 years, with internal audits required annualy.during the years between formal external audits.
Sanitary stainless welding certification
Sanitary stainless welding certification requires strict conformance to hygienic welding guidelines and uses a specific approved welding method — gas tungsten arc welding (GTAW), otherwise known asor tungsten inert gas (TIG) welding. These standards are essential for welds used by medical, pharmaceutical, biotech and food industries for health and safety reasons. A rough surface on a weld isn’t a problem an issue for most applications. A weld on a lawnmower that’s not silky smooth isn’t likely to impact the lawnmower’s performance or safety so long as the weld is strong.
However, welds for the food, dairy, and drug industries must be completely smooth and seamless. Any roughness or pitting on or around the weld is difficult to sanitize and can create an environment for microbial contamination and growth. Rough edges may also be more likely to corrode, which would compromise the integrity and contaminate the product could contaminate consumable products. An unsanitary weld could also cause damage and likelihood of degradation to surfaces near the weld, not just in the weld itself.
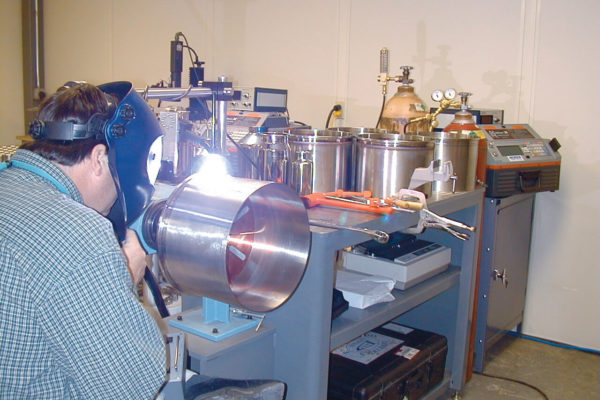
Material traceability standards
According to the American Institute of Steel Construction, traceability for steel means the “ability to identify a specific piece of steel in a structure, throughout the life of the structure, and its specific mill test report (MTR).” ISO standards define traceability as the “ability to trace the history, application, use and location of an item or its characteristics through recorded identification data.” Being able to trace products from the raw materials to final consumption helps protect the safety of retail consumers. If something goes wrong with a product, it can be traced back to its origin so that the problem can be fixed or at least contained.
It also protects businesses who use the stainless steel during other manufacturing processes, assuring them that the grade of steel in the item they are purchasing is correct for the intended application. All stainless steel has an iron and chromium base, but there are differences in the additional alloy components of various series and grades. To qualify as a specific grade, a piece of stainless steel must have the correct percentages of that grade’s alloy materials. A specific mill test report verifies that the steel has exactly the correct materials and percentages for its grade, as well as documenting other information about the stainless steel. It can include information such as the material’s dimensions, heat number/code, and mechanical properties as well as the chemical analysis of the steel.
One reason this information is important is because grades of steel vary in how they perform under certain circumstances. For example, the 400 series of grades is exceptionally durable for high-friction applications and works well for motors and gears. The 300 series, which contains nickel specific elements and additional chromium, is more resistant to chemicals, salts, and acids. Since this means it can resist both chemicals used during frequent sanitation and salts and acids in foods and medications, this series produces most food-grade and medical-grade steel.
MTR material traceability standards report
According to the American Institute of Steel Construction, traceability for steel means the “ability to identify a specific piece of steel in a structure, throughout the life of the structure, and its specific mill test report (MTR).” ISO standards define traceability as the “ability to trace the history, application, use and location of an item or its characteristics through recorded identification data.” Being able to trace products from the raw materials to final consumption helps protect the safety of retail consumers.
If there is a future issue with a product, it can be traced back to its origin so that the problem can be fixed or at least contained. It also protects businesses who use the stainless steel during other manufacturing processes, assuring them that the grade of steel in the item they are purchasing is correct for the intended application.
Eagle Stainless can provide a material traceability reports (mill certifications) which documents the lifecycle of a product – including raw materials used to create it, who manufactured it, and where it is distributed – whether it’s used to in the manufacture of other products or sold as an individual piece. Identification is one part of traceability – having a consistent method of identifying a product. Raw materials used in stainless steel fabrication have heat numbers/codes to identify which batch of metal they came from, while fabricated stainless steel products usually have serial numbers or lot numbers.
Laser etching can create a permanent identification method for stainless steel parts and products, making them easier to trace. The other part of traceability involves documentation of the part or product throughout its lifecycle – creating the paper trail. Both ASME and ISO look at a fabricator’s processes and documentation as part of their certification audits, and manufacturers must maintain a system of storing and maintaining this data for at least three years.